As an Amazon Associate, I earn from qualifying purchases. Be careful though, too much tension can flatten your wire. (These angles do not include your travel angle, which well talk about next.). The following article will go into detail on how to set the voltage on a MIG welder.
These settings also determine the transfer type for metal deposition. Some wire and gas combinations commonly seen with MIG welding are: You choose your wire size by the amperage setting, which in turn depends on material thickness. If you've ever had a sunburn you know how painful it can be. If you started with a weld that only needed 0.6mm wire and then changed to a weld that needed 1mm wire, youd need to change liners. Therefore, you have to know how thick your metal is.
On the other hand, if youre moving too slowly or you have too much wire being fed through, youre going to have a fat weld join that will need to be ground back, causing a lack of fusion on the toes (edges of the weld). Depending on your circumstances this could result in a terrible-looking weld and make the welder sputter. Unfortunately, MIG isnt as forgiving as stick welding, so youll need to either wire brush or grind your workpiece so that its clean. Sometimes you will hear a popping sound. Now that the wire spool is attached inside the machine, feed it through the torch until it sticks out of the torch nozzle. That is one of the key determining factors of amperage setting on a MIG welder. Ive included a chart below to help you select your voltage by inspecting the bead. How big is the job? While it is true that if you are not a professional welder it may be hard to know if the voltage of your MIG welder is set properly.
Check that your earth clamp has been attached to a metal surface, such as a (clean) metal workbench or the workpiece, because if your earth clamp isnt grounded, your machine wont start. It will change based on the joint, thickness of the metal. If youre using a shielding gas for your weld, there are a few to choose from, as different metals require different shields. Watch your weld puddle and inspect your beads. One of those details is setting the right parameters on your new MIG welder for the job at hand. Whether youre pushing or pulling, you want to keep your torch at a 10 to 15 angle. However, if theres too much gas pressure at the weld, you can draw oxygen into the arc plasma and contaminate the bead, causing porosity. If youre making a fillet join, you can use a magnetic welding clamp to hold your two pieces of metal together. Different materials have different characteristics related to heat and electricity. MIG welding itself is relatively easy once youve got the hang of your angles and speed; all you need to do is press the trigger and start pushing or pulling your weld along the joint. It is getting too much current and causing damage. Fully screw down the liner retaining nut and nip it up tight.
These look like a small round bump and dent, respectively. Once youve run your weld along the joint, youre done. Both parts screw on and off with ease, so theres no hassle. The push technique directs the heat away from the weld puddle, allowing faster travel speeds and providing a flatter weld profile with light penetration useful for welding thin materials. Reduce the voltage and you will have more control over the weld. Pretty cool, right? This compresses the liner inside the torch cable assembly preventing it from moving during use and ensures good wire feed. It may be a disappointment to some, finding out theres no quick, easy answer to the questions youre grappling with.
O.K. Being able to identify this is something that takes a bit of experience, but if something is really wrong, youll notice pretty fast. There are a few factors that will influence the type of welding that will work best for you. Listen and watch closely as you weld. If your angle becomes too deep or parallel with the metal youre welding, you increase the spatter amount, decrease penetration, and create more mess that youll have to clean up later. Thank you for the useful article and please keep up the fine work.
These basic settings are: You want to create the right heat conditions at the weld to run a smooth arc, eliminate spatter and maximize penetration. Quality welding equipment makes things easier. Related read: MIG Welding Gas Pressure Setting. These choices are heavily influenced by material composition and thickness. This is simply a place to start. While some machines are limited to gas or gasless only, at UNIMIG, all of our MIG welders are capable of both processes. Disclaimer: Weldguru.com is based on information from multiple sources including U.S. Army Operator Circulars, O.S.H.A and our own first hand experience with welding. You may need to change your liner before you feed your wire through, as these liners much like the rollers will only fit specific sizes. Onboard digital menus and input variables like material type and thickness, will set the MIG welder up automatically. Take this information and these charts not as gospel nor as science. Pull the trigger again while holding the wire. The voltage setting will also change depending on the size of the electrode that you use and the type of gas you are using. To replace a roller, unscrew the retaining cap and take the old roller off. This gives you some choice about what works best for your welder and your technique. There are three main types of materials that are common for welding. If youre trying to weld thicker pieces of metal together, adjust your volts and wire speed accordingly. Unfortunately, you wont be able to rewind it because itll no longer be precision wound, and therell be a much higher chance that the wire will birdnest inside the wire feed mechanism, halting your weld. Tacks are used to fuse the metals together at the edges, so you dont have to hold them together while youre trying to weld. Once youre happy with your performance on a dry run, try it again on some scrap metal before you move on to the piece youre planning on welding. This is where your spool gun comes in. If the wire sticks out too far, trim it back. Wire feed speed (WFS) affects your heat level. Before you can even start, you have to choose the right process and take care of the mechanical and technical setup. Aluminium isnt magnetic, however, so a manual clamp will be needed. Is there an AWS spec somewhere?
A higher voltage gives a flatter deeper weld. Your work angle is your torch in relation to the angle of the joint. This technique offers a better view of the weld joint and direction of the wire into the weld joint. The wire is located at the leading edge of the weld pool and pushed towards the un-melted work surface. For good results, its necessary to use the right shielding gas and electrode. I did find myself wrestling with some undercut near the end of my welds.wish I had steady hands and eyes OK thanksnow it makes sense why I could not find any AWS reference regards the subject. link to Why Do Welders Wear Jeans - 5 Reasons to Wear Jeans, link to Can Welding Give You a Tan or Sunburn - Complete Guide. The kind of wire you are using will determine the technique required when welding. You want to move at a speed that corresponds with your settings. The neck spring keeps the liner ridged so it can be fed into the torch with no issues and keeps the wire from kinking. Travel speed is how fast you are moving the torch along the weld. Thank You Sir!
When determining amperage, you will also need to know the thickness of the material. If youre using mild steel, stainless steel or aluminium, youll want to travel at a pushing angle (torch over the weld pool pushing towards the metal).
I concur with Steve above. The result will be an unattractive weld. I've personally experienced this several times over the years. When youre using gas, all you need to do is attach the regulator to the tank, attach the gas hose from the welding machine to the regulator and set your gas flow. If youre shielding gas is being blown away, then the weld will be prone to defects like porosity (the Swiss cheese look).
and as John said, run your focus mainly on the heavier plate, and let the puddle wash in rhythm onto the 1/4 plate. This way, less current can make the same weld in one pass. Regardless of whether you are using gas or gasless wire, your earth clamp will need to be attached to your workpiece (the metal youre welding) or something metal that will conduct to your workpiece nearby; otherwise, the machine wont weld. You can see how it may affect the control and penetration of your weld. The voltage setting will determine your arc length.
If youre moving too fast for your set wire speed, then therell be nothing being fed into the weld pool to create a proper weld. But leave a door open, and a draft may blow the gas away at that rate, so you need to go to 35 CFM, for example. You are probably here for this reason, so Ill explain the main MIG settings and how they should be adjusted. Second, manufacturers indulge in a little bit of magic to get these numbers to advertise performance.
Once youve lined them up, slide your spool onto the shaft and screw your nut back in to lock the spool into place. Those parameters are set to the application involved. This distance is called Electrode Stickout (ESO), and its a limiting factor. Voltage determines how high and how wide the bead is. In other words, trial and error. If you do need to change it, then you must unbolt the internal leads and adjust them manually. How is that possible? The most common is ferrous vs. non-ferrous materials. Hopefully, the question.
Specifically, the link thats supposed to allow the reader to print a full-size chart that can actually be used.
If youre going to use a standard MIG torch for an aluminium wire, youll need an aluminium specific liner (in the correct size). MIG welders are usually CV (constant voltage). Each of these material types will require different amperage. Higher feed rates allow better contact between the wire and weld puddle. He has always been interested in welding from an early age and has the cuts and bruises to prove it as he set out to work with a variety of metals. Jeff Grill hails from Long Island, a 118 mile stretch of land that starts just off the coast of Manhattan and stretches deep into the Atlantic ocean. As was stated previously, voltage controls the arc length between the pool of molten metal and the wire point. Always try to remember the importance of maintaining your voltage so you can remain in control of your weld and your welding project. If you hear a slower popping sound it is often based on the wire feed. Youll need to feed the first part of the wire into the inlet guide, over the roller and into the beginning of the guide tube before you let go of it to stop it from unravelling. UNIMIG recommends an 8-12L per minute gas flow rate for all MIG welding, and these recommended settings can be found on the guide table inside each machine. Before you begin, its essential that the filler metal you purchase matches the metal you plan to weld (your parent metal). Every UNIMIG welding machine comes with a User Manual and Setup Guide, which provides a good starting point for your machine settings. There is no one set that fits every welding scenario. You just have to pay attention. Higher concentrations of helium or argon make for a hotter arc. The second problem is that your shielding gas will no longer be able to reach your weld pool, and youll increase the number of defects like porosity in your weld. That type of precise settings for volts, amps/wire feed speed is not dealt with in the D1 codes.
You may also be able to find the correct voltage chart on the company website of your machine.if(typeof ez_ad_units!='undefined'){ez_ad_units.push([[300,250],'welderslab_com-leader-1','ezslot_7',111,'0','0'])};if(typeof __ez_fad_position!='undefined'){__ez_fad_position('div-gpt-ad-welderslab_com-leader-1-0')}; There is no one set that works all the time. Ive been welding for the last 20 years and running my own welding business for the last 10 years. The second is gasless, and the filler metal used has a flux core, which protects the weld instead of gas. Read more about MIG transfer types here. That is why we say it is the most commonly used knob on a welding machine. It makes very good welds on 110v c-25 but is set for c-20 not c-25 and also has a setting for c02 but I couldnt get my c02 bottle exchanged here.. You can feed the wire through in two ways; hold down the trigger on the torch or press the feed wire button inside the machine. It matters a great deal what material youre welding. The arc and heat are concentrated on the weld pool. It may also create a poor tie-in at the toes of the weld. Depending on the thickness of the materials, the job site where you are working, and what type of project you are working on, the voltage and amperage can change. How do I set the voltage on a MIG welder has been answered for you.
Another question people ask when they set the voltage on a MIG welder is what happens if you set your voltage too high? Carefully pull out and completely remove the existing liner. Hi Jeff ~ I see that the last update was on July 8, 2022, so seeing that its only 5 days later, I assume that youre maintaining this article. It could also create excessive spatter which can be a safety hazard. They are the main metal found around the home and in cars. By its very nature, handcrafting isnt scientific. You set the amperage according to the thickness of the metal. You will also need a higher amperage because of the higher melting point of aluminum. You want to maintain the 1cm of stickout throughout the joint for the best weld.
They bevel the edges of the joint to get the thickness down. These are all things to consider when deciding which type of welder youll need. Always test your settings on a scrap piece of metal. Mild steel, aluminum, and stainless or nickel alloys are the most used metals with the MIG process. That is because it causes the insulator to stop insulating. These are only guidelines. Its a good idea to have something to steady your hands against as they go along the weld so that you can maintain your angle and distance. The main thing that your welds position will affect is whether or not youll be fighting against gravity as you go. Practice makes perfect. Although your welder may have a nice selection of adjustments, its important to understand that most of them are for fine-tuning. Place your cleaned workpiece in front of you in a way that when you begin welding, your hands can move freely and steadily all the way along the joint. To get great welding results that are repeatable your metal needs to ready to work on. The welds are wider and flatter, allowing for minimal clean up/grinding time. The gas is used to shield the weld metal from any outside contaminants when welding. clean the surface really well, the mill scale can contribute to under cut. MIG welding torches come with a Euro connection that plugs directly into the front of the machine. This liner goes in and out the same way as steel liners, but you have to attach a neck spring on the top of the liner before inserting it. You see, the weld will get wider and flatter if you have too high of a voltage. Voltage level and feed rate need to be balanced against each other. If the weld is just for practice, it doesnt matter how good it looks. The spool holder can only hold 1kg rolls, so if youre doing a lot of aluminium welding, itll run out faster than in a machine, and the gun is going to fatigue your hands faster. Place the new roller on (lining up the keyway on the roller with the key on the machine) and re-screw the retaining nut. Some MIG welders automate most of the settings process which makes it easier to set up. Each roller comes with two grooves; these are the wire sizes (e.g. 0.6mm & 0.8mm). I applied your recommended settings to my MIG.
Lets use an example. It may also make the weld stand taller or thinner, another thing you do not want when you are MIG welding. There are a lot of people out there with welding machines who dont have formal training. Know the thickness of the metal so you know if your welder has the power to get the job done, you can choose the right electrode wire and the proper shielding gas. The gun and wire are pulled away from the weld bead. Fit the liner retaining nut and screw only 1/2 way down. Settings for dirty metal dont apply to clean metal, Less oil or paint to catch fire means less to think about. For instance, the difference between steel and aluminum. This means that you need to insert the polarity cable into the Positive (+) panel mount and the earth clamp (which comes provided) into the Negative () panel mount. If youre welding with aluminium, then youll need pure argon for your shielding gas. Ill mention aluminum or other materials whenever theyre relevant. Maybe when things are still, 5 CFM is enough to shield the weld properly. Dont use too much angle and also, watch the wetting. You want your wire to stick out of the torch nozzle by roughly 1cm. I have been trying to chase down, what seems to me to be, the elusive answer to the subject.
When it comes to welding, its the nature of the game, Im afraid. We will examine what happens if you set the voltage too high or too low. If the feed rate is low, the weld area can run too cool for good penetration. Side Note: The general rule is that the thicker your metal is the higher the voltage will be. Remember to flip your welding helmet down before you ignite your arc. Remember, welding voltage is primarily to control the arc length. So whether youre looking to tinker around or start your own welding shop youre in the right place. If you are not a professional welder, it may be hard to know if your MIG welder is set to the proper voltage. Save my name, email, and website in this browser for the next time I comment.
Theres no stopping it; its just a more difficult metal. The arc length is the distance between the pool of molten metal and the wire at the point of the arc. Gas welding with aluminium, stainless steel, and mild steel all require an electrode positive polarity. The main difference between these three torch types is that they were initially made by different manufacturers. Bearing this in mind, Id appreciate it if you would fix the link thats mentioned below the MIG Welding Settings Chart Wire Speed & Voltage chart. Here are the most-used wire sizes in MIG welding. I think thats great, but there is one drawback. If youre welding outdoors with gas, youll find you may need to turn up the gas flow or set up a cover, as the breeze can affect how much gas is reaching the weld pool. Lock the tension lever and decrease the tension by rotating counter-clockwise so that the wire slips (the rollers are spinning, but the wire doesnt move) when the trigger is pulled. Another problem with too low voltage is that it could result in a convex bead profile. Heliarc Welding Explained: What Is It? Some machines have a burnback function that allows you to determine the wires burnback after your finish welding as well. Keep in mind, consulting your owners manual is always a good idea.
This is why MIG welding is considered one of the easiest types of welding to learn and a great place to start for beginners. We respect your privacy and promise not to spam. It will contain the most important information you need to properly set the voltage on your MIG welder. Gas is metered in cubic feet per minute (CFM), and drafts, breezes, or cylinder temperatures affect the results. Check out our MIG Welders Guide for information about some of these machines. Observe the bead, keep your eyes open for splatter, and listen for popping sounds so you can adjust to the circumstances of the project. This is separate from the wire speed, but the two do impact each other. Once youve sorted your tension, trim any excess wire hanging out of the tip. Titanium Unlimited 140 Review Is It Worth It? The starting voltage type will almost always be Direct Current Electrode Positive. Increasing the current level and creating too much heat results in spattering. It is the most commonly used welder setting knob on your machine in the middle of a job. Why Do Welders Wear Jeans - 5 Reasons to Wear Jeans. Settings dont create good welds; they just make good welds possible. Hi Jeff, Not sure if you still maintain this or not but just wanted to let you know I found your information extremely helpfull.

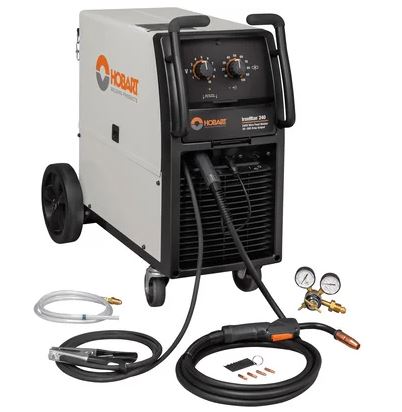
Check that your earth clamp has been attached to a metal surface, such as a (clean) metal workbench or the workpiece, because if your earth clamp isnt grounded, your machine wont start. It will change based on the joint, thickness of the metal. If youre using a shielding gas for your weld, there are a few to choose from, as different metals require different shields. Watch your weld puddle and inspect your beads. One of those details is setting the right parameters on your new MIG welder for the job at hand. Whether youre pushing or pulling, you want to keep your torch at a 10 to 15 angle. However, if theres too much gas pressure at the weld, you can draw oxygen into the arc plasma and contaminate the bead, causing porosity. If youre making a fillet join, you can use a magnetic welding clamp to hold your two pieces of metal together. Different materials have different characteristics related to heat and electricity. MIG welding itself is relatively easy once youve got the hang of your angles and speed; all you need to do is press the trigger and start pushing or pulling your weld along the joint. It is getting too much current and causing damage. Fully screw down the liner retaining nut and nip it up tight.

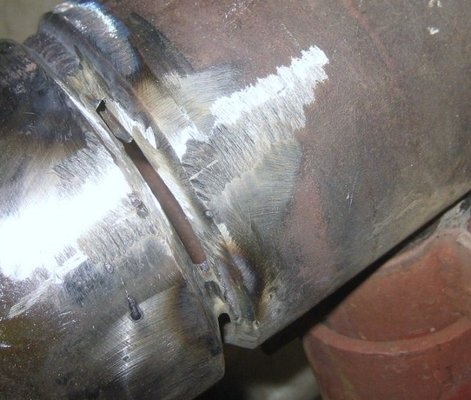
These basic settings are: You want to create the right heat conditions at the weld to run a smooth arc, eliminate spatter and maximize penetration. Quality welding equipment makes things easier. Related read: MIG Welding Gas Pressure Setting. These choices are heavily influenced by material composition and thickness. This is simply a place to start. While some machines are limited to gas or gasless only, at UNIMIG, all of our MIG welders are capable of both processes. Disclaimer: Weldguru.com is based on information from multiple sources including U.S. Army Operator Circulars, O.S.H.A and our own first hand experience with welding. You may need to change your liner before you feed your wire through, as these liners much like the rollers will only fit specific sizes. Onboard digital menus and input variables like material type and thickness, will set the MIG welder up automatically. Take this information and these charts not as gospel nor as science. Pull the trigger again while holding the wire. The voltage setting will also change depending on the size of the electrode that you use and the type of gas you are using. To replace a roller, unscrew the retaining cap and take the old roller off. This gives you some choice about what works best for your welder and your technique. There are three main types of materials that are common for welding. If youre trying to weld thicker pieces of metal together, adjust your volts and wire speed accordingly. Unfortunately, you wont be able to rewind it because itll no longer be precision wound, and therell be a much higher chance that the wire will birdnest inside the wire feed mechanism, halting your weld. Tacks are used to fuse the metals together at the edges, so you dont have to hold them together while youre trying to weld. Once youre happy with your performance on a dry run, try it again on some scrap metal before you move on to the piece youre planning on welding. This is where your spool gun comes in. If the wire sticks out too far, trim it back. Wire feed speed (WFS) affects your heat level. Before you can even start, you have to choose the right process and take care of the mechanical and technical setup. Aluminium isnt magnetic, however, so a manual clamp will be needed. Is there an AWS spec somewhere?
A higher voltage gives a flatter deeper weld. Your work angle is your torch in relation to the angle of the joint. This technique offers a better view of the weld joint and direction of the wire into the weld joint. The wire is located at the leading edge of the weld pool and pushed towards the un-melted work surface. For good results, its necessary to use the right shielding gas and electrode. I did find myself wrestling with some undercut near the end of my welds.wish I had steady hands and eyes OK thanksnow it makes sense why I could not find any AWS reference regards the subject. link to Why Do Welders Wear Jeans - 5 Reasons to Wear Jeans, link to Can Welding Give You a Tan or Sunburn - Complete Guide. The kind of wire you are using will determine the technique required when welding. You want to move at a speed that corresponds with your settings. The neck spring keeps the liner ridged so it can be fed into the torch with no issues and keeps the wire from kinking. Travel speed is how fast you are moving the torch along the weld. Thank You Sir!
When determining amperage, you will also need to know the thickness of the material. If youre using mild steel, stainless steel or aluminium, youll want to travel at a pushing angle (torch over the weld pool pushing towards the metal).
I concur with Steve above. The result will be an unattractive weld. I've personally experienced this several times over the years. When youre using gas, all you need to do is attach the regulator to the tank, attach the gas hose from the welding machine to the regulator and set your gas flow. If youre shielding gas is being blown away, then the weld will be prone to defects like porosity (the Swiss cheese look).
and as John said, run your focus mainly on the heavier plate, and let the puddle wash in rhythm onto the 1/4 plate. This way, less current can make the same weld in one pass. Regardless of whether you are using gas or gasless wire, your earth clamp will need to be attached to your workpiece (the metal youre welding) or something metal that will conduct to your workpiece nearby; otherwise, the machine wont weld. You can see how it may affect the control and penetration of your weld. The voltage setting will determine your arc length.
If youre moving too fast for your set wire speed, then therell be nothing being fed into the weld pool to create a proper weld. But leave a door open, and a draft may blow the gas away at that rate, so you need to go to 35 CFM, for example. You are probably here for this reason, so Ill explain the main MIG settings and how they should be adjusted. Second, manufacturers indulge in a little bit of magic to get these numbers to advertise performance.
Once youve lined them up, slide your spool onto the shaft and screw your nut back in to lock the spool into place. Those parameters are set to the application involved. This distance is called Electrode Stickout (ESO), and its a limiting factor. Voltage determines how high and how wide the bead is. In other words, trial and error. If you do need to change it, then you must unbolt the internal leads and adjust them manually. How is that possible? The most common is ferrous vs. non-ferrous materials. Hopefully, the question.
Specifically, the link thats supposed to allow the reader to print a full-size chart that can actually be used.
If youre going to use a standard MIG torch for an aluminium wire, youll need an aluminium specific liner (in the correct size). MIG welders are usually CV (constant voltage). Each of these material types will require different amperage. Higher feed rates allow better contact between the wire and weld puddle. He has always been interested in welding from an early age and has the cuts and bruises to prove it as he set out to work with a variety of metals. Jeff Grill hails from Long Island, a 118 mile stretch of land that starts just off the coast of Manhattan and stretches deep into the Atlantic ocean. As was stated previously, voltage controls the arc length between the pool of molten metal and the wire point. Always try to remember the importance of maintaining your voltage so you can remain in control of your weld and your welding project. If you hear a slower popping sound it is often based on the wire feed. Youll need to feed the first part of the wire into the inlet guide, over the roller and into the beginning of the guide tube before you let go of it to stop it from unravelling. UNIMIG recommends an 8-12L per minute gas flow rate for all MIG welding, and these recommended settings can be found on the guide table inside each machine. Before you begin, its essential that the filler metal you purchase matches the metal you plan to weld (your parent metal). Every UNIMIG welding machine comes with a User Manual and Setup Guide, which provides a good starting point for your machine settings. There is no one set that fits every welding scenario. You just have to pay attention. Higher concentrations of helium or argon make for a hotter arc. The second problem is that your shielding gas will no longer be able to reach your weld pool, and youll increase the number of defects like porosity in your weld. That type of precise settings for volts, amps/wire feed speed is not dealt with in the D1 codes.
You may also be able to find the correct voltage chart on the company website of your machine.if(typeof ez_ad_units!='undefined'){ez_ad_units.push([[300,250],'welderslab_com-leader-1','ezslot_7',111,'0','0'])};if(typeof __ez_fad_position!='undefined'){__ez_fad_position('div-gpt-ad-welderslab_com-leader-1-0')}; There is no one set that works all the time. Ive been welding for the last 20 years and running my own welding business for the last 10 years. The second is gasless, and the filler metal used has a flux core, which protects the weld instead of gas. Read more about MIG transfer types here. That is why we say it is the most commonly used knob on a welding machine. It makes very good welds on 110v c-25 but is set for c-20 not c-25 and also has a setting for c02 but I couldnt get my c02 bottle exchanged here.. You can feed the wire through in two ways; hold down the trigger on the torch or press the feed wire button inside the machine. It matters a great deal what material youre welding. The arc and heat are concentrated on the weld pool. It may also create a poor tie-in at the toes of the weld. Depending on the thickness of the materials, the job site where you are working, and what type of project you are working on, the voltage and amperage can change. How do I set the voltage on a MIG welder has been answered for you.
Another question people ask when they set the voltage on a MIG welder is what happens if you set your voltage too high? Carefully pull out and completely remove the existing liner. Hi Jeff ~ I see that the last update was on July 8, 2022, so seeing that its only 5 days later, I assume that youre maintaining this article. It could also create excessive spatter which can be a safety hazard. They are the main metal found around the home and in cars. By its very nature, handcrafting isnt scientific. You set the amperage according to the thickness of the metal. You will also need a higher amperage because of the higher melting point of aluminum. You want to maintain the 1cm of stickout throughout the joint for the best weld.
They bevel the edges of the joint to get the thickness down. These are all things to consider when deciding which type of welder youll need. Always test your settings on a scrap piece of metal. Mild steel, aluminum, and stainless or nickel alloys are the most used metals with the MIG process. That is because it causes the insulator to stop insulating. These are only guidelines. Its a good idea to have something to steady your hands against as they go along the weld so that you can maintain your angle and distance. The main thing that your welds position will affect is whether or not youll be fighting against gravity as you go. Practice makes perfect. Although your welder may have a nice selection of adjustments, its important to understand that most of them are for fine-tuning. Place your cleaned workpiece in front of you in a way that when you begin welding, your hands can move freely and steadily all the way along the joint. To get great welding results that are repeatable your metal needs to ready to work on. The welds are wider and flatter, allowing for minimal clean up/grinding time. The gas is used to shield the weld metal from any outside contaminants when welding. clean the surface really well, the mill scale can contribute to under cut. MIG welding torches come with a Euro connection that plugs directly into the front of the machine. This liner goes in and out the same way as steel liners, but you have to attach a neck spring on the top of the liner before inserting it. You see, the weld will get wider and flatter if you have too high of a voltage. Voltage level and feed rate need to be balanced against each other. If the weld is just for practice, it doesnt matter how good it looks. The spool holder can only hold 1kg rolls, so if youre doing a lot of aluminium welding, itll run out faster than in a machine, and the gun is going to fatigue your hands faster. Place the new roller on (lining up the keyway on the roller with the key on the machine) and re-screw the retaining nut. Some MIG welders automate most of the settings process which makes it easier to set up. Each roller comes with two grooves; these are the wire sizes (e.g. 0.6mm & 0.8mm). I applied your recommended settings to my MIG.
Lets use an example. It may also make the weld stand taller or thinner, another thing you do not want when you are MIG welding. There are a lot of people out there with welding machines who dont have formal training. Know the thickness of the metal so you know if your welder has the power to get the job done, you can choose the right electrode wire and the proper shielding gas. The gun and wire are pulled away from the weld bead. Fit the liner retaining nut and screw only 1/2 way down. Settings for dirty metal dont apply to clean metal, Less oil or paint to catch fire means less to think about. For instance, the difference between steel and aluminum. This means that you need to insert the polarity cable into the Positive (+) panel mount and the earth clamp (which comes provided) into the Negative () panel mount. If youre welding with aluminium, then youll need pure argon for your shielding gas. Ill mention aluminum or other materials whenever theyre relevant. Maybe when things are still, 5 CFM is enough to shield the weld properly. Dont use too much angle and also, watch the wetting. You want your wire to stick out of the torch nozzle by roughly 1cm. I have been trying to chase down, what seems to me to be, the elusive answer to the subject.
When it comes to welding, its the nature of the game, Im afraid. We will examine what happens if you set the voltage too high or too low. If the feed rate is low, the weld area can run too cool for good penetration. Side Note: The general rule is that the thicker your metal is the higher the voltage will be. Remember to flip your welding helmet down before you ignite your arc. Remember, welding voltage is primarily to control the arc length. So whether youre looking to tinker around or start your own welding shop youre in the right place. If you are not a professional welder, it may be hard to know if your MIG welder is set to the proper voltage. Save my name, email, and website in this browser for the next time I comment.
Theres no stopping it; its just a more difficult metal. The arc length is the distance between the pool of molten metal and the wire at the point of the arc. Gas welding with aluminium, stainless steel, and mild steel all require an electrode positive polarity. The main difference between these three torch types is that they were initially made by different manufacturers. Bearing this in mind, Id appreciate it if you would fix the link thats mentioned below the MIG Welding Settings Chart Wire Speed & Voltage chart. Here are the most-used wire sizes in MIG welding. I think thats great, but there is one drawback. If youre welding outdoors with gas, youll find you may need to turn up the gas flow or set up a cover, as the breeze can affect how much gas is reaching the weld pool. Lock the tension lever and decrease the tension by rotating counter-clockwise so that the wire slips (the rollers are spinning, but the wire doesnt move) when the trigger is pulled. Another problem with too low voltage is that it could result in a convex bead profile. Heliarc Welding Explained: What Is It? Some machines have a burnback function that allows you to determine the wires burnback after your finish welding as well. Keep in mind, consulting your owners manual is always a good idea.
This is why MIG welding is considered one of the easiest types of welding to learn and a great place to start for beginners. We respect your privacy and promise not to spam. It will contain the most important information you need to properly set the voltage on your MIG welder. Gas is metered in cubic feet per minute (CFM), and drafts, breezes, or cylinder temperatures affect the results. Check out our MIG Welders Guide for information about some of these machines. Observe the bead, keep your eyes open for splatter, and listen for popping sounds so you can adjust to the circumstances of the project. This is separate from the wire speed, but the two do impact each other. Once youve sorted your tension, trim any excess wire hanging out of the tip. Titanium Unlimited 140 Review Is It Worth It? The starting voltage type will almost always be Direct Current Electrode Positive. Increasing the current level and creating too much heat results in spattering. It is the most commonly used welder setting knob on your machine in the middle of a job. Why Do Welders Wear Jeans - 5 Reasons to Wear Jeans. Settings dont create good welds; they just make good welds possible. Hi Jeff, Not sure if you still maintain this or not but just wanted to let you know I found your information extremely helpfull.