(1986). According to the comparison with the experimental results, the accuracy of the model is verified. Therefore, for heat conduction calculation of vapor space, the key is to solve the equivalent thermal conductivity of this subregion. 35).
The experimental system for high-temperature heat pipe is established to verify the proposed model. The comparison of calculated results between experimental results (Poston, 2017). For example, for wick with a mesh type, the density, specific heat capacity, and thermal conductivity can be approximately described by Eqs 57 (Chi, 1976). This model can be used for heat pipe cooled reactor simulation. Zuo ignored the temperature drop caused by the vapor flow and considered that the temperature drop of the heat pipe was mainly caused by the heat conduction in wall and wick. (2013) proposed a simplified method to consider the evaporation, condensation, and backflow (Figure 3). Thermal Performance Analysis of Nanofluids in a Thermosyphon Heat Pipe Using CFD Modeling. Heat generated in the reactor core is absorbed by high-temperature heat pipes. Core thermal-hydraulic Evaluation of a Heat Pipe Cooled Nuclear Reactor. uv is vapor velocity, Ladia is the length of adiabatic section, and Lcond is the length of condenser. Considering the high temperature of the condenser section, not only the natural convection, but the radiation heat transfer also exist. Temperature distribution of heat pipe (3000W). During the steady state analysis (section 4.2), the boundary of the condenser section is set as the fixed temperature. 142, 107412. doi:10.1016/j.anucene.2020.107412, Ma, Y., Chen, E., Yu, H., Zhong, R., Deng, J., Chai, X., et al. To meet the requirements of heat pipe cooled reactor simulation, the super thermal conductivity model (STCM) is proposed. Then, the temperature is recorded with the increase of heating power.
Detailed view of the KRUSTY reactor system (Poston et al., 2020). (1973). Using commercial codes such as FLUENT and CFX, the modeling difficulty can be greatly simplified, and built-in advanced numerical algorithms can ensure the stability of numerical calculation as much as possible.
A Transient Multiphysics Coupling Method Based on OpenFOAM for Heat Pipe Cooled Reactors[J]. 10:819033. doi: 10.3389/fenrg.2022.819033. At about T = 300.0s, fuel reaches the peak temperature of about 1,080.3K. At about T = 2,200.0s, the reactor reaches the new steady state. For radiation of wall, it is treated as the radiant heat transfer to infinite space (Eq. (B) Network model. Chi, S. W. (1976). to go back to the article page.Or contact our
To ensure the accuracy of temperature data, the groove with 1mm depth is processed in wall. HPTAMheatpipe Transient Analysis Model: an Analysis of Water Heat Pipes. Wang, C., Sun, H., Tang, S., Tian, W., Qiu, S., and Su, G. (2020).
Moreover, for reactor systems with higher power density and more complex heat pipe arrangement, it can be expected that the temperature non-uniform effect of the contact surface will have a more significant impact on the operation of the reactor. Wall is usually a cylindrical closed shell made of metal. Figure 7A shows the surface temperature distribution with different heating powers, and Figure 7B shows the temperature variation of heat pipe with time. For heat pipe, it includes the wall, the wick, and the vapor space. doi:10.1016/s0017-9310(97)00220-2, Keywords: heat pipe cooled reactor, high-temperature heat pipe, STCM, heating system, KRUSTY reactor, Citation: Guo Y, Su Z, Li Z and Wang K (2022) The Super Thermal Conductivity Model for High-Temperature Heat Pipe Applied to Heat Pipe Cooled Reactor. Three-dimensional CFD model of the experimental system.
Using the network method, the flow of working medium is approximately accounted for. Thermal-hydraulic Analysis of a New Conceptual Heat Pipe Cooled Small Nuclear Reactor System. For load-following transient calculation, calculated results are in good agreement with the experimental results, showing the applicability of the proposed model to this type of reactor system. ScienceDirect is a registered trademark of Elsevier B.V. Click here to go back to the article page. Copyright 2022 Guo, Su, Li and Wang. 149, 107755. doi:10.1016/j.anucene.2020.107755, Mcclure, P. R. (2015). Simulation of the Early Startup Period of High-Temperature Heat Pipes from the Frozen State by a Rarefied Vapor Self-Diffusion Model[J].
who will be happy to help. The network system for heat pipe operation. doi:10.1115/1.3604687, Li, H., Jiang, X., Chen, L., Ning, Y., Pan, H., and Tengyue, M. (2015). Theoretical Investigation of Heat Pipes Operating at Low Vapor Pressures. is the emissivity of material, and is the Stefan-Boltzmann coefficient. Heat pipes using alkali metal can realize efficient heat transport in special environments with high temperature (Faghri, 2014). Meanwhile, to ensure the safety of heat transport, there are a large number of high-temperature heat pipes in the reactor core. The Stirling generators are also ignored, the operation of generators is approximated by setting reasonable boundary conditions of the condenser section of heat pipes. Tech. Wick is composed of a porous structure and liquified working medium. Phys. Using a high-temperature adhesive, all K-type armored thermocouples are fixed in the groove (Figure 5A). doi:10.1016/0017-9310(73)90260-3, Cao, Y., and Faghri, A. All authors contributed to manuscript revision, read, and approved the submitted version. So far, proposed conceptual designs of heat pipe cooled reactor systems include the kilopower reactor system (McClure et al., 2020a), the Heatpipe-Operated Mars Exploration Reactor (HOMER) system (Poston, 2001), and the Heat Pipe-segmented Thermoelectric Module Converters Space Reactor (HP-STMCs) system (El-Genk and Tournier, 2004). Energ. 15 (3), 759772. The uncertainty of an experimental system is inevitable. From Figure 8B, it can also be found that although there is an insulating layer wrapped outside the adiabatic section, the high-temperature vapor will still be partially condensed in this section, resulting in the reduction of vapor flow rate in vapor space. Heat Transfer 114 (4), 10281035. From that, it can be concluded that there is a slight difference between the two results, and proposed model is suitable for the analysis of heat pipe cooled reactor system. Nucl.
Sonic Limitations and Startup Problems of Heat Pipes. Tech. The difference between two results can be approximately considered to be caused by the uncertainty of parameters used in the model and the uncertainty of the experimental system. Minsk, Belarus: CIS. Los Alamos, NM (United States): Los Alamos National Lab, Poston, D. I. Lumped Parameter Model of Sintered Heat Pipe: Transient Numerical Analysis and Validation. doi:10.1063/1.41777. When the heat transfer limitations occur, the heat transfer capacity of heat pipe will significantly reduce. The comparison between simulated results using the proposed model and experimental results shows in Figure 15. FIGURE 1. For reactor systems with a solid attribute, heat conductance is the only way for heat transfer. National Institute of Space Research (INPE), Brazil. Eng. doi:10.1115/1.2910657, Cao, Y., and Faghri, A. Heat Pipe Transient Response Approximation. Figure 12 shows the fuel temperature distribution using the proposed model and network model. KRUSTY Experiment: Reactivity Insertion Accident Analysis. For example, the network model cannot consider the nonuniform heat transfer between the heat pipe and the environment. In addition, Zuo ignored the energy transport caused by the backflow of working medium in wick. Detailed Transient Model of a Liquid-Metal Heat Pipe. Generally, the convective heat transfer coefficient obtained from equation (Eq. (1967). Therefore, the basis of coupling calculation on this type of reactor system is to have a suitable model for high-temperature heat pipe simulation. The difference between the two values is the heat leakage through shield. Therm. Int. This model does not directly calculate the vapor flow in the vapor space, however, the evaporation, the condensation, and vapor flow rate can be obtained using the simplified method mentioned in Section 2.2.2. Los Alamos, NM (United States): Los Alamos National Lab. According to the comparison, it is found that the temperature calculated by this model differs little from the experimental results. doi:10.1007/s00231-013-1110-6, Brown, O. L. I. Forms of it include channels, screen, and concentric annulus (Reay et al., 2013).
Aiaa J. In the future, further numerical analysis and experimental studies will be carried out to investigate the real characteristics of heat pipe when the heat transfer limitation occurs. KRUSTY Reactor Design. Space Nuclear Reactor Engineering. The boundary temperature of the condenser of heat pipes is set as 1,052.0K, and the fission power is set as 5.0kW. Study on Startup Characteristics of Heat Pipe Cooled and AMTEC Conversion Space Reactor System. Heat Transfer Capacity Analysis of Heat Pipe for Space Reactor[J]. Phenomena such as vapor flow and vapor-liquid interface shape variation are not important for the safety analysis of heat pipe cooled reactor. doi:10.1016/j.applthermaleng.2018.01.011, Zuo, Z. J., and Faghri, A. To verify the proposed model, a heating system for high-temperature heat pipe is built (Figure 4). The reason for this phenomenon is the uneven power distribution in space. Numer. J. Chem. Three boundary conditions (Eqs 24) can be selected for heat transfer: where Q is the heating source, A is the surface area, h is the convective coefficient, T(i) is the surface temperature of wall, and T is the environment temperature. Energ. During startup, the drastic variation of vapor density, pressure, and velocity may lead to numerical instability. 86, 1830. In the steady state calculation, the results show that the temperature distribution on contact surface between fuel and heat pipe is nonuniform, which will lead to higher peak temperature and temperature difference for the reactor core. To simplify the modeling, the lift table and support structure are all ignored; only the reactor is established (Figure 11). doi:10.1080/10407789008944804, Cao, Y., and Faghri, A. doi:10.1080/00295450.2020.1722554. (A) T = 0.0s. It is assumed that vapor in vapor space and liquified working medium in wick are homogeneous. The typical heat pipe cooled reactor named KRUSTY is chosen as the research object. When the heating power is high enough, the increase of total temperature difference will become inconspicuous, which means heat pipe has entered the optimal working range. The electric heater is simplified as the thin layer with a thickness of 2mm, and the heating source is set in this layer as equivalent to an electrical heating. doi:10.1016/j.ijheatmasstransfer.2012.09.007, Liu, X., Zhang, R., Liang, Y., Tang, S., Wang, C., Tian, W., et al. At. Based on Fouriers law, higher heat flux will lead to a larger temperature gradient, resulting in non-uniformity of temperature distribution on the contact surface. In this paper, the super thermal conductivity model (STCM) for high-temperature heat pipe is proposed, which simplifies the vapor flow and heat transport in vapor space into heat conductance. Therefore, the heat pipe models at this period were based on some reasonable assumptions. Combined with the network method, the evaporation rate, the condensation rate, and the flow rate in the wick region can be preliminarily obtained. Heat pipe processing for heating experiments. Therm. Copyright 2020 Elsevier B.V. or its licensors or contributors. The key to the realization of this model is to determine the thermophysical parameters and heating source of each subregion. Using this model, the numerical simulation on KRUSTY reactor is executed. Department of Engineering Physics, Tsinghua University, Beijing, China. It should be noted that the two-phase flow simulation using CFD method requires large amounts of computing resources. Thermionic Conversion Specialist Conference, United States, November 1-2, 1967, 391398. Heat Mass Transfer 57 (2), 642656. Or contact our Benefiting from the reactivity feedback of fuel, fission power gradually decreases to slow the rate of temperature rise.
Inst. Am. (1993). The heating system for high-temperature heat pipe is established to validate this model. The proposed model can calculate the variation of absorbed power of heat pipes. Design of Megawatt Power Level Heat Pipe Reactors. Eng. FIGURE 12. The equation that needs to be solved is the differential equation of heat conduction (Eq. (1951). CFD Simulation on the Heat Transfer and Flow Characteristics of a Microchannel Separate Heat Pipe under Different Filling Ratios. 1), S43S55. 14, Eqs 2123, the total pressure drop can be determined. (2020). The applicability of this model will be discussed. The backflow of working medium is treated as a heating source in a differential equation of heat conduction. Proc. In the early stage of this accident, the reactor will be briefly supercritical, resulting in the increase in reactor power. Industry. Tech. Thermionic Conversion Specialist Conference, This article is part of the Research Topic, https://doi.org/10.3389/fenrg.2022.819033. 1), S1S12. 1): where is the density, C is the specific heat capacity, T is the temperature, is the thermal conductivity coefficient, and H is the volumetric heating source. A Numerical Analysis of High-Temperature Heat Pipe Startup from the Frozen State. Basic constitution of a heat pipe cooled reactor (Mcclure, 2015). Theory of the Ultimate Heat Transfer Limit of Cylindrical Heat Pipes. doi:10.1080/00295450.2020.1722544, McClure, P. R., Poston, D. I., Gibson, M. A., Mason, L. S., and Robinson, R. C. (2020). Due to these characteristics, high-temperature heat pipe is widely used for the design of heat pipe cooled reactor systems. Power density distribution along axial distribution.
Combined with the network method, the evaporation, condensation, and backflow can be obtained (Ferrandi et al., 2013). During this accident, with the decrease of engine power, heat transport power of heat pipes also reduces, leading to the increase of fuel temperature. Eng. support team who will be happy to help. In general, due to the nonuniformity of reactor power distribution and the directionality of coolant flow in the heat exchanger, the actual heat transport and temperature distribution of each heat pipe are different. Closed-form Analytical Solutions of High-Temperature Heat Pipe Startup and Frozen Startup Limitation. Ann. On the one hand, to realize the coupling calculation of the heat pipe cooled reactor, the proposed heat pipe model does not directly calculate the working fluid circulation, but adopts a simplified method, which may cause uncertainty to a certain extent. Therefore, it is important for the numerical calculation of heat pipe cooled reactor to obtain the accurate temperature distribution as much as possible. In the transient calculation, the load-following accident is chosen. The three-dimensional CFD model of the experimental system is shown in Figure 6, which includes the sodium heat pipe, the electric heater, and the insulating layer. AIP Conf. If the calculated value is less than the heating power, the heat transfer limitation will be deemed to occur, and it is assumed that the heat pipe will be damaged. 10 (1), 83114. 33) is not completely equal to the real value.
The experimental system for high-temperature heat pipe is established to verify the proposed model. The comparison of calculated results between experimental results (Poston, 2017). For example, for wick with a mesh type, the density, specific heat capacity, and thermal conductivity can be approximately described by Eqs 57 (Chi, 1976). This model can be used for heat pipe cooled reactor simulation. Zuo ignored the temperature drop caused by the vapor flow and considered that the temperature drop of the heat pipe was mainly caused by the heat conduction in wall and wick. (2013) proposed a simplified method to consider the evaporation, condensation, and backflow (Figure 3). Thermal Performance Analysis of Nanofluids in a Thermosyphon Heat Pipe Using CFD Modeling. Heat generated in the reactor core is absorbed by high-temperature heat pipes. Core thermal-hydraulic Evaluation of a Heat Pipe Cooled Nuclear Reactor. uv is vapor velocity, Ladia is the length of adiabatic section, and Lcond is the length of condenser. Considering the high temperature of the condenser section, not only the natural convection, but the radiation heat transfer also exist. Temperature distribution of heat pipe (3000W). During the steady state analysis (section 4.2), the boundary of the condenser section is set as the fixed temperature. 142, 107412. doi:10.1016/j.anucene.2020.107412, Ma, Y., Chen, E., Yu, H., Zhong, R., Deng, J., Chai, X., et al. To meet the requirements of heat pipe cooled reactor simulation, the super thermal conductivity model (STCM) is proposed. Then, the temperature is recorded with the increase of heating power.
Detailed view of the KRUSTY reactor system (Poston et al., 2020). (1973). Using commercial codes such as FLUENT and CFX, the modeling difficulty can be greatly simplified, and built-in advanced numerical algorithms can ensure the stability of numerical calculation as much as possible.
A Transient Multiphysics Coupling Method Based on OpenFOAM for Heat Pipe Cooled Reactors[J]. 10:819033. doi: 10.3389/fenrg.2022.819033. At about T = 300.0s, fuel reaches the peak temperature of about 1,080.3K. At about T = 2,200.0s, the reactor reaches the new steady state. For radiation of wall, it is treated as the radiant heat transfer to infinite space (Eq. (B) Network model. Chi, S. W. (1976). to go back to the article page.Or contact our
To ensure the accuracy of temperature data, the groove with 1mm depth is processed in wall. HPTAMheatpipe Transient Analysis Model: an Analysis of Water Heat Pipes. Wang, C., Sun, H., Tang, S., Tian, W., Qiu, S., and Su, G. (2020).


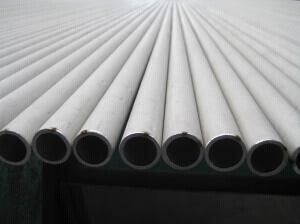

Aiaa J. In the future, further numerical analysis and experimental studies will be carried out to investigate the real characteristics of heat pipe when the heat transfer limitation occurs. KRUSTY Reactor Design. Space Nuclear Reactor Engineering. The boundary temperature of the condenser of heat pipes is set as 1,052.0K, and the fission power is set as 5.0kW. Study on Startup Characteristics of Heat Pipe Cooled and AMTEC Conversion Space Reactor System. Heat Transfer Capacity Analysis of Heat Pipe for Space Reactor[J]. Phenomena such as vapor flow and vapor-liquid interface shape variation are not important for the safety analysis of heat pipe cooled reactor. doi:10.1016/j.applthermaleng.2018.01.011, Zuo, Z. J., and Faghri, A. To verify the proposed model, a heating system for high-temperature heat pipe is built (Figure 4). The reason for this phenomenon is the uneven power distribution in space. Numer. J. Chem. Three boundary conditions (Eqs 24) can be selected for heat transfer: where Q is the heating source, A is the surface area, h is the convective coefficient, T(i) is the surface temperature of wall, and T is the environment temperature. Energ. During startup, the drastic variation of vapor density, pressure, and velocity may lead to numerical instability. 86, 1830. In the steady state calculation, the results show that the temperature distribution on contact surface between fuel and heat pipe is nonuniform, which will lead to higher peak temperature and temperature difference for the reactor core. To simplify the modeling, the lift table and support structure are all ignored; only the reactor is established (Figure 11). doi:10.1080/10407789008944804, Cao, Y., and Faghri, A. doi:10.1080/00295450.2020.1722554. (A) T = 0.0s. It is assumed that vapor in vapor space and liquified working medium in wick are homogeneous. The typical heat pipe cooled reactor named KRUSTY is chosen as the research object. When the heating power is high enough, the increase of total temperature difference will become inconspicuous, which means heat pipe has entered the optimal working range. The electric heater is simplified as the thin layer with a thickness of 2mm, and the heating source is set in this layer as equivalent to an electrical heating. doi:10.1016/j.ijheatmasstransfer.2012.09.007, Liu, X., Zhang, R., Liang, Y., Tang, S., Wang, C., Tian, W., et al. At. Based on Fouriers law, higher heat flux will lead to a larger temperature gradient, resulting in non-uniformity of temperature distribution on the contact surface. In this paper, the super thermal conductivity model (STCM) for high-temperature heat pipe is proposed, which simplifies the vapor flow and heat transport in vapor space into heat conductance. Therefore, the heat pipe models at this period were based on some reasonable assumptions. Combined with the network method, the evaporation rate, the condensation rate, and the flow rate in the wick region can be preliminarily obtained. Heat pipe processing for heating experiments. Therm. Copyright 2020 Elsevier B.V. or its licensors or contributors. The key to the realization of this model is to determine the thermophysical parameters and heating source of each subregion. Using this model, the numerical simulation on KRUSTY reactor is executed. Department of Engineering Physics, Tsinghua University, Beijing, China. It should be noted that the two-phase flow simulation using CFD method requires large amounts of computing resources. Thermionic Conversion Specialist Conference, United States, November 1-2, 1967, 391398. Heat Mass Transfer 57 (2), 642656. Or contact our Benefiting from the reactivity feedback of fuel, fission power gradually decreases to slow the rate of temperature rise.
Inst. Am. (1993). The heating system for high-temperature heat pipe is established to validate this model. The proposed model can calculate the variation of absorbed power of heat pipes. Design of Megawatt Power Level Heat Pipe Reactors. Eng. FIGURE 12. The equation that needs to be solved is the differential equation of heat conduction (Eq. (1951). CFD Simulation on the Heat Transfer and Flow Characteristics of a Microchannel Separate Heat Pipe under Different Filling Ratios. 1), S43S55. 14, Eqs 2123, the total pressure drop can be determined. (2020). The applicability of this model will be discussed. The backflow of working medium is treated as a heating source in a differential equation of heat conduction. Proc. In the early stage of this accident, the reactor will be briefly supercritical, resulting in the increase in reactor power. Industry. Tech. Thermionic Conversion Specialist Conference, This article is part of the Research Topic, https://doi.org/10.3389/fenrg.2022.819033. 1), S1S12. 1): where is the density, C is the specific heat capacity, T is the temperature, is the thermal conductivity coefficient, and H is the volumetric heating source. A Numerical Analysis of High-Temperature Heat Pipe Startup from the Frozen State. Basic constitution of a heat pipe cooled reactor (Mcclure, 2015). Theory of the Ultimate Heat Transfer Limit of Cylindrical Heat Pipes. doi:10.1080/00295450.2020.1722544, McClure, P. R., Poston, D. I., Gibson, M. A., Mason, L. S., and Robinson, R. C. (2020). Due to these characteristics, high-temperature heat pipe is widely used for the design of heat pipe cooled reactor systems. Power density distribution along axial distribution.
Combined with the network method, the evaporation, condensation, and backflow can be obtained (Ferrandi et al., 2013). During this accident, with the decrease of engine power, heat transport power of heat pipes also reduces, leading to the increase of fuel temperature. Eng. support team who will be happy to help. In general, due to the nonuniformity of reactor power distribution and the directionality of coolant flow in the heat exchanger, the actual heat transport and temperature distribution of each heat pipe are different. Closed-form Analytical Solutions of High-Temperature Heat Pipe Startup and Frozen Startup Limitation. Ann. On the one hand, to realize the coupling calculation of the heat pipe cooled reactor, the proposed heat pipe model does not directly calculate the working fluid circulation, but adopts a simplified method, which may cause uncertainty to a certain extent. Therefore, it is important for the numerical calculation of heat pipe cooled reactor to obtain the accurate temperature distribution as much as possible. In the transient calculation, the load-following accident is chosen. The three-dimensional CFD model of the experimental system is shown in Figure 6, which includes the sodium heat pipe, the electric heater, and the insulating layer. AIP Conf. If the calculated value is less than the heating power, the heat transfer limitation will be deemed to occur, and it is assumed that the heat pipe will be damaged. 10 (1), 83114. 33) is not completely equal to the real value.